Selecting and Using the Right Grease
Using the proper lubricant can increase machine performance and lifespan
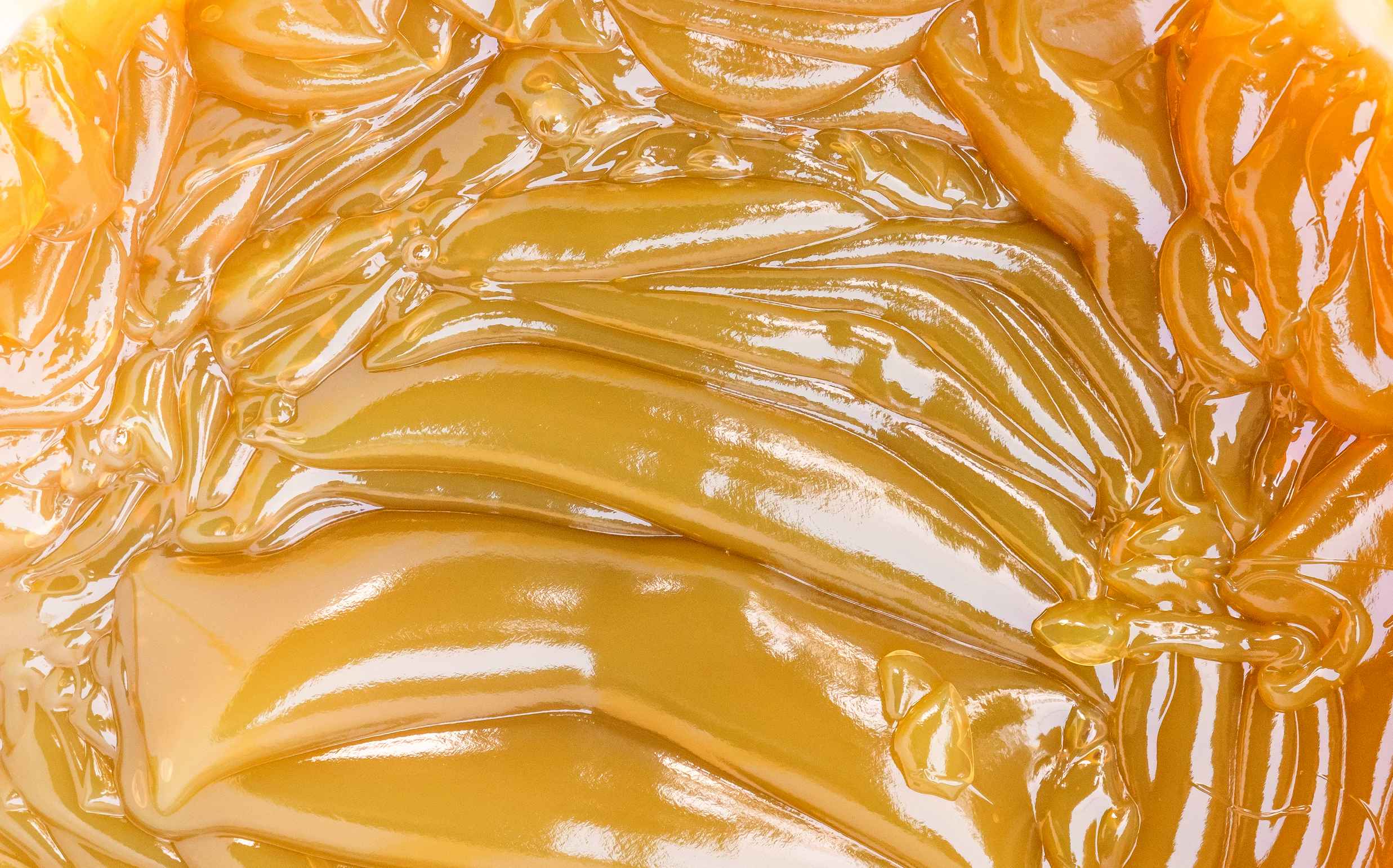
The primary purpose of grease, as with most lubricants, is to reduce the friction between moving machine components to reduce wear, act as a contamination barrier and as a vehicle for heat transfer. When applied correctly and at the appropriate intervals, according to Noria Corporation, grease can increase machine performance and lifespan.
Information from the provider of consulting and training services on machinery lubrication for Fortune 500 companies worldwide details grease selection and other best practices. The white paper was sponsored by Citgo Lubricants and Mystik Lubricants.
Why Grease Selection and Best Practices Are Important
Different lubricants serve different functions. It’s essential to select a grease suited to your specific application. The health of a machine depends on the health of the lubricant. An inferior grease may fail before it is scheduled to be replaced, leading to machine wear. At the same time, the longevity and qualities of a grease are diminished unless proper maintenance techniques are in place.
Standards and categorizations for grease are set by the National Lubricating Grease Institute (NLGI). Greases are categorized based on their relative hardness and ability to resist deformation from outside forces, factors that are represented by the grease’s NGLI consistency number (NLGI grade).
Heavy-duty grease is designed for applications that typically submit machinery to heavier loads. These greases have additives that can help separate and even soften machine component surfaces, preventing them from welding together.
“Not all grease is created equal,” emphasized Jonathan Roberts, vice president and general council for Lube-a-Boom. “Different moving components of machinery will often require a different type of grease, and not all greases are created equal. Greases have different grades, different soaps, additives, etc. that all work together to provide lubrication for the component.”
Choosing a Grease Type
Generally, a specific type of grease will be recommended by the original equipment manufacturer (OEM).
“For example, a good wire rope grease should be able to penetrate to the rope’s core (where most wire rope failures occur) but also provide an outside coating of lubrication to protect against friction and the elements,” Roberts added. “An open gear lubricant, for example, would not achieve those goals and wouldn’t be the best option for a wire rope.”
To select the right grease, consider:
- Base oil viscosity is one of the most important attributes of a lubricating grease. Typically, speed factors are used to determine the minimum and optimum viscosity requirements.
- Thickener type, which determines a grease’s optimum consistency for a given application is based on operating temperature and speed factors.
- Additive packages should be selected based on factors specific to each application. For example, heavy-load applications will require a grease with extreme pressure additives (EP), while a high-speed application will not.
A high-quality, heavy-duty grease will be designed to handle a wide variety of heavy-duty applications. Optimized blends of mineral and synthetic oils can be combined with complex thickener systems to produce greases with:
- Excellent wear control
- Water resistance
- High extreme pressure performance
- Superior corrosion protection
Grease Best Practices and Regreasing Calculations
It is not enough to select the right grease; you must also perform proactive maintenance to ensure the grease is performing at an optimum level. Regreasing intervals should be set and should be adhered to as closely as possible. Waiting until a machine shows signs of problems before regreasing means it is too late to prevent damage.
There are many factors that influence when regreasing intervals should be set. Readily available online calculators can be used to determine the optimal frequency of regreasing and the amount of grease needed.
When regreasing, it is important to remove the old grease. This old grease will likely contain some level of contamination, which, if allowed to contact the new grease, will transfer and corrupt the new grease.
Additionally, the old and new greases may be incompatible, either due to different levels of viscosity or certain additives.
It is also important to use the correct amount of grease. Over greasing can be just as damaging as under greasing or not adding grease at all. If too much grease is added to a component like a bearing, it can overfill the bearing cavity, forcing grease to leak from seals and opening avenues for contamination and moisture ingression.
Ensure that zerks are kept clean before regreasing. These fittings can become covered in grease, allowing dirt to stick to exposed surfaces. If this dirt build-up is not wiped away before regreasing, it can be dragged into the machine with the new grease.
Other Considerations
Grease dry-out is one of the main disadvantages of using grease instead of oil. Grease tends to cake together and dry out, causing the oil held within the grease to bleed out. Grease dry-out can be caused by:
- Contamination
- Mechanical wring out
- Incompatible greases
- Thermal run-away
- Base oil oxidation
- High temperature violability
- Hydrostatic exhaustion
- Vibration and centrifugal forces
Weather, and more specifically temperature, can affect the performance of grease. Viscosity is beholden to changes in temperatures, and as weather changes, temps must be considered.
The need for heavy-duty greases is amplified in applications and environments that are extremely demanding on machinery. Choosing the right grease, and implementing it properly, optimizes machine performance and extends asset longevity.